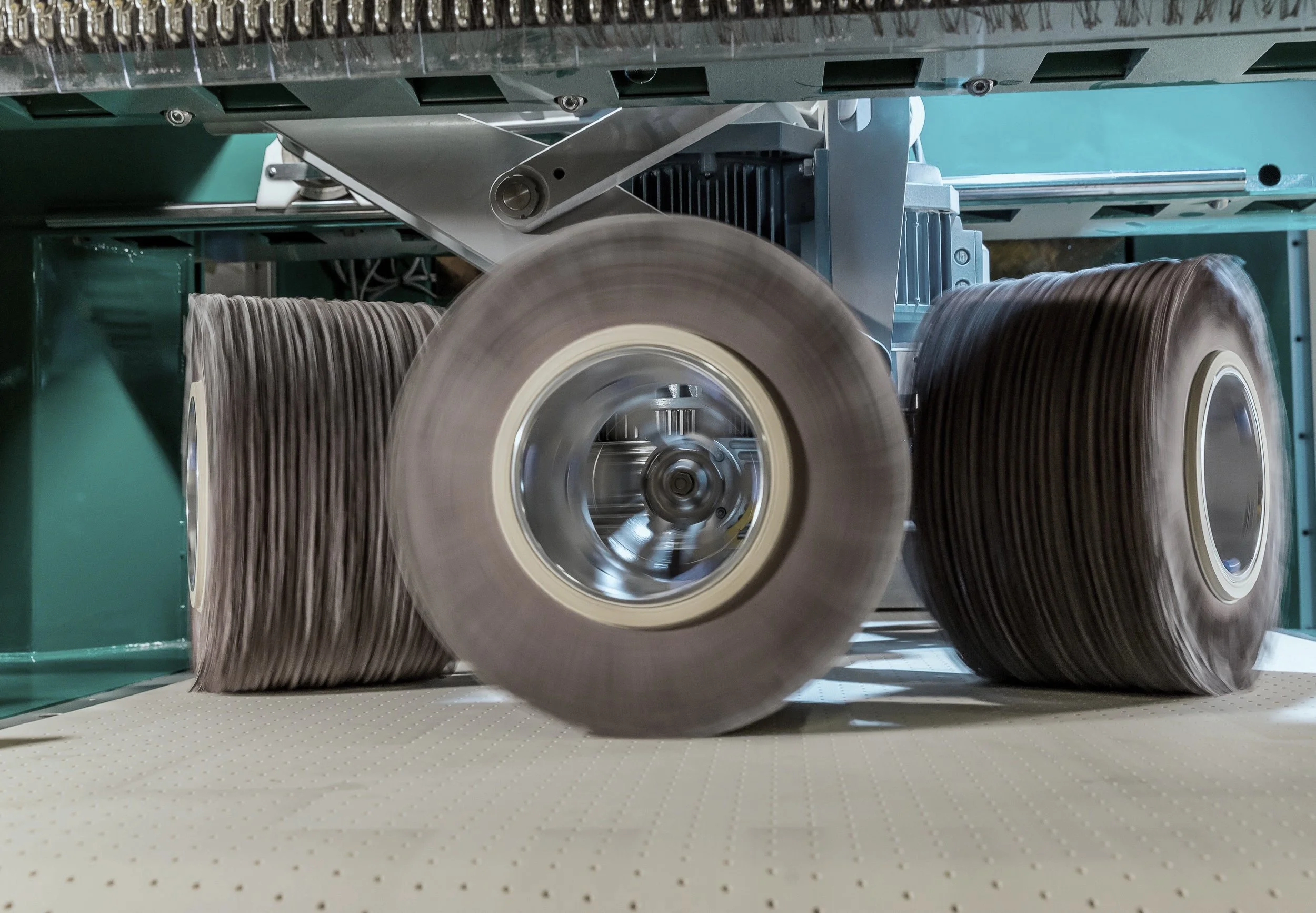
DEBURRING
>> effective removal of burrs for a smooth surface.
Deburring capabilities
-
Deburring
In our Fladder® Gyro 300 deburring machine, we edge round and surface grind metals and other materials with excellent results. A 2 mm radius can be achieved in most materials. All edges are accessible from all directions. On flat surfaces, the grinding pattern becomes completely irregular.
-
Max Material Size
1300 mm (w) x unlimited (l)
-
Thickness
Up to 100 mm.
>> Very efficient deburring
>> Removes burrs from all angles
>> Can create significant edge rounding
>> Provides a surface with an irregular sanding pattern
Deburring, oscillating grinding technique.
The Fladder® technique allows deburring without damaging protective plastics, meaning that deburring can be done without harming surface patterns such as hairline grinding or anodized/oxidized surfaces. Deburring of 3D objects is also often possible.
Deburring is an important process for removing unwanted edges or burrs from processed materials and products. This can be crucial for achieving optimal quality and functionality in the final product. A common method for deburring is using a Fladder®, a rotating brush machine that can process a wide variety of materials.
Fladder® deburring is an efficient and precise method for removing irregularities and edges from processed materials. Fladder® is often used in the metal and wood industries, but it can also be used for other materials, such as plastics and composites.
Fladder® deburring uses a rotating drum with soft abrasive discs mounted on its surface. The discs are made of soft fibers, allowing them to grind without damaging the surface of the processed material. As the drum rotates, the discs grind away irregularities and edges from the material’s surface. Because the discs are flexible, they can also grind uneven areas on difficult and complex surfaces, making it a versatile method for deburring.
One advantage of Fladder® deburring is its versatility. Fladder® can be used to deburr a wide range of materials, including metal, wood, plastic, and composites. It can also be used to create various textures and surfaces on the processed material, such as matte, polished, or brushed finishes.
An important factor to consider in Fladder® deburring is selecting the correct type of discs for the processed material. The discs come in various sizes and materials to suit different materials and applications. By choosing the right type of discs, you can achieve optimal results and avoid damage to the processed material.
scandcut.com
-
The powerful and compact grinding head is equipped with a total of six spindles, which rotate in pairs clockwise and counterclockwise. The spindles are separately driven in pairs to avoid localized grinding of materials and uneven wear of the grinding tool.
During the grinding process, the entire grinding head rotates with the six grinding spindles, while also oscillating over the parts. This means that the surface is processed from all possible angles, regardless of where the parts are placed on the conveyor belt.
-
Deburring is an important process for removing unwanted edges or burrs from processed materials and products. This can be crucial for achieving optimal quality and functionality in the final product. A common method for deburring is using a Fladder®, a rotating brush machine that can process a variety of materials.
-
Metals, plastics, composites and ceramic materials.